For businesses operating multiple plants, the intricacies of managing supply chains can often feel like navigating a labyrinth. With countless variables at play—from fluctuating demand to transportation delays—ensuring timely shipments and optimal resource allocation becomes crucial to staying ahead of the competition. But fear not! Native American Logistics has the information you need about the best practices that can transform your multi-plant operations into well-oiled machines. Through innovative strategies and cutting-edge tools, you’ll learn how to streamline your supply chain processes, reduce costs, enhance visibility, and improve customer satisfaction.
Introduction to Multi-Plant Operations and Supply Chain Management
Multi-plant operations bring unique challenges that require a strategic approach to optimizing shipments. As businesses expand their footprint across regions, the complexity of logistics increases exponentially.
The need for seamless communication, real-time tracking, and effective planning becomes paramount. Companies must navigate these hurdles while still meeting customer expectations for timely deliveries and cost-effective solutions. With so many moving parts involved in 3PL optimizing freight, how can organizations streamline their processes? Let’s explore best practices that not only enhance operational efficiency but also lead to significant savings on shipping costs. Get ready to transform your multi-plant operations into a well-oiled machine!
Understanding the Challenges of Optimizing Shipments in Multi-Plant Operations
Multi-plant operations present a unique set of challenges when it comes to optimizing shipments. Each facility has its own processes, capacities, and supply chain dynamics. This complexity often leads to inefficiencies.
Communication becomes fragmented across plants. Without centralized data sharing, teams struggle to coordinate effectively. Delays can occur as information moves slowly between locations.
Additionally, fluctuations in demand can create confusion. When one plant experiences a surge in orders while another faces a lull, maintaining balance becomes difficult.
Logistics also play a crucial role. Coordinating transportation routes and schedules among multiple sites requires careful planning and execution.
Lastly, differing regulations or standards across regions may hinder smooth operations. Navigating these discrepancies adds another layer of difficulty that companies must address for effective shipment optimization within their multi-plant setups.
Best Practices for Streamlining Supply Chains in Multi-Plant Operations
Streamlining supply chains in multi-plant operations is essential for improving efficiency, reducing costs, and meeting customer demands. Companies can achieve this by adopting key strategies such as centralizing communication, utilizing real-time tracking, implementing lean principles, leveraging forecasting tools, and consolidating shipments.
-
Centralize Communication and Data Sharing
Centralized communication ensures all stakeholders have access to the same data, fostering collaboration and informed decision-making. It reduces silos between plants and provides visibility into inventory levels, production schedules, and shipping updates. This transparency enables better planning and faster responses to disruptions. To centralize effectively, businesses should invest in user-friendly platforms, establish clear protocols for data sharing, and provide thorough training to employees. Addressing challenges such as system compatibility and data security is also critical to success.
-
Use Real-Time Tracking and Monitoring Systems
Real-time tracking enhances visibility across the supply chain by providing updates on shipment locations and statuses. This technology enables companies to identify potential bottlenecks or delays, allowing for prompt corrective action. It also supports better inventory management by providing accurate data on stock levels at various locations. Additionally, historical data analysis through these systems helps optimize transportation routes, reducing costs and improving delivery efficiency. Adopting real-time tracking ensures compliance with regulatory requirements and enhances customer satisfaction through accurate and timely deliveries.
-
Implement Lean Principles
Lean principles focus on reducing waste and improving efficiency. In multi-plant operations, this includes eliminating unnecessary steps, optimizing shipment routes, and reducing manual tasks. Continuous improvement, a cornerstone of lean, involves regularly reviewing processes to identify areas for refinement. Lean principles also emphasize customer value by tailoring operations to meet their needs, such as consolidating shipments to lower costs. Building a culture of teamwork across departments and utilizing tools like 5S methodology further enhances supply chain efficiency.
-
Utilize Forecasting and Planning Tools
Forecasting tools enable companies to predict demand accurately, helping them maintain optimal inventory levels and avoid overstocking or stockouts. Supply chain planning software integrates various aspects of the supply chain, from raw material procurement to transportation logistics. Real-time data analysis supports informed decision-making, while collaboration platforms improve coordination between departments. Advanced analytics, such as predictive modeling, identify potential delays and ensure proactive resolution, optimizing the overall supply chain process.
-
Consolidate and Coordinate Shipments
Consolidating shipments reduces transportation costs by combining orders into larger loads, benefiting from economies of scale. Coordinating shipment timing among plants minimizes expenses and avoids unnecessary delays. Consolidation also reduces administrative tasks, streamlines logistics, and supports environmental sustainability by lowering emissions. Effective communication between plants and careful planning are essential to address challenges like compatibility issues and scheduling conflicts.
By implementing these best practices, companies can streamline supply chains in multi-plant operations, improving efficiency, reducing costs, and enhancing customer satisfaction. Continuous evaluation and adaptation of these strategies ensure businesses remain competitive in an ever-evolving market.
Case Study:
Success Story of a Company that Optimized Shipments in Multi-Plant Operations
One notable success story comes from a leading manufacturer in the automotive industry. Faced with rising costs and delays, they turned to optimizing their multi-plant operations.
By implementing advanced real-time tracking systems, they gained visibility across their supply chain. This transparency allowed for quicker decision-making regarding shipments and inventory levels.
Additionally, they centralized communication between plants. This collaboration led to improved coordination of shipments and reduced lead times significantly.
Their use of forecasting tools also played a crucial role. Accurate demand predictions helped them plan better, preventing overstocking or shortages at different facilities.
As a result, this company not only slashed operational costs but also enhanced customer satisfaction through timely deliveries. Their commitment to innovation set a benchmark in multi-plant shipment optimization that others now aspire to achieve.
Potential Pitfalls to Avoid in Optimizing Shipments in Multi-Plant Operations
Optimizing shipments in multi-plant operations is a complex process, fraught with challenges. Key pitfalls include a lack of collaboration between facilities, failure to adapt to demand fluctuations or supply chain disruptions and neglecting the power of data analytics. Native American Logistics is ready to help you overcome these obstacles and ensure efficiency and cost savings.
-
Eliminating the Silo Effect: Fostering Collaboration
The “silo effect,” where plants operate independently without collaboration, is a significant barrier to optimization. The first step in breaking down silos is aligning all plants toward shared supply chain goals. When managers recognize their interdependence, they are more likely to coordinate efforts to achieve mutual success.
Improved communication is vital. Technologies like shared dashboards or regular video conferences facilitate real-time information sharing about production schedules, inventory levels, and demand forecasts. This transparency ensures timely decision-making based on accurate data.
Clear role definitions and responsibilities among plant managers are equally important. When accountability is established, decision-making is streamlined, and cooperation improves. Incentives tied to overall supply chain performance, rather than individual plant metrics, can also motivate cross-functional teamwork and foster a culture of continuous improvement.
Technology plays a critical role in fostering collaboration. Advanced software solutions provide visibility into operations across plants, identifying bottlenecks and enabling proactive solutions. By aligning goals, improving communication, and leveraging technology, companies can eliminate silos and optimize multi-plant operations.
-
Addressing Communication Gaps
A common challenge in multi-plant supply chains is the lack of effective communication and collaboration. Silos result in disruptions, delays, and increased costs. Miscommunication often arises from inadequate communication channels or unclear protocols, leaving teams unaware of each other’s roles and processes.
Real-time visibility is crucial. Without access to data on inventory levels, production schedules, or transportation capabilities, plants struggle to plan shipments effectively. This can create a ripple effect, where disruptions at one facility negatively impact others.
To address these issues, companies must prioritize collaboration. Cross-functional teams, standardized communication protocols, and technologies like enterprise resource planning (ERP) systems can bridge gaps, enhance visibility, and enable efficient decision-making. Such measures streamline supply chains and improve coordination between facilities.
-
Adapting to Fluctuations
The inability to adapt to changing demand or supply chain disruptions is another pitfall. Rigid systems can lead to overstocking or stockouts, eroding profitability and customer satisfaction.
To mitigate this, regular cross-plant meetings enable better forecasting and planning. Centralized data management systems offer visibility into inventory levels and production schedules, allowing for proactive adjustments. Maintaining open communication with suppliers ensures responsiveness to changing needs, while establishing relationships with backup suppliers adds resilience.
Technology, such as real-time tracking tools, supports faster decision-making by providing actionable insights into order statuses, transportation schedules, and inventory levels. By embracing adaptability, companies can navigate fluctuations effectively and maintain operational efficiency.
-
Effective Oversight
Effective oversight is integral to optimizing multi-plant operations. Understanding each plant’s unique requirements, such as lead times and delivery schedules, ensures smooth coordination.
Consolidating shipments from geographically close plants reduces transportation costs and minimizes inefficiencies. Real-time inventory data enables managers to prioritize shipments based on demand forecasts, avoiding delays caused by overstocking or stockouts.
Collaboration with suppliers and the use of transportation management systems (TMS) enhances oversight. TMS provides shipment visibility and analytics for continuous improvement, supporting seamless operations.
By addressing these pitfalls and adopting best practices, companies can transform multi-plant supply chains into streamlined, efficient systems that drive success. Contact a representative at Native American Logistics today so we can streamline your multi-plant supply chain. Contact us today.
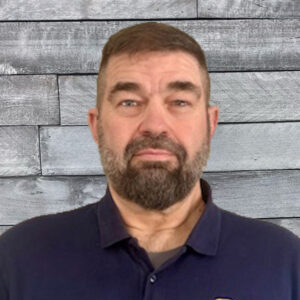
Jeff Berlin
is the Chief Operating Officer of E.L. Hollingsworth & Co. and serves as the Senior Operations Executive for TOP Worldwide and Native American Logistics. With over 30 years of experience leading logistics and trucking companies, he brings deep industry expertise to his role. Jeff is also a CDL-A driver and a private pilot. Contact Jeff at jberlin@elhc.net.